PLC Electronic Basics
PLC Electronic Basics
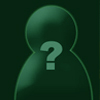
Electronic Basics in Relation to the PLC
Before diving into developing control software for a PLC, you need to understand at least the basics of electricity: I won’t be diving into that too deeply as it goes beyond the scope of this document and there is a great deal of information available online: So if you want to know the theory and calculations such as Ohms law, Google: What I will be going over is the basics needed in order to understand PLC development:
First a little history: Before PLC’s came about, controls were done by an array of relays: A relay is nothing more than a switch that is controlled electro-magnetically: I won’t get into too much detail because: well Google will help keep this document from being ridiculously long: But, basically when you apply power to a relay, it powers up the electro-magnet and mechanically moves a rocker arm that will either provide continuity or completely remove continuity: They are arranged in variations of poles and throws: Think of the pole as the path that provides continuity and the throw as the direction of continuity: You have a huge variety of relay types, but some of the most common are:
- SPST: Single Pole, Single Throw:
- SPDT: Single Pole, Double Throw:
- DPST: Double Pole, Single Throw:
- DPDT: Double Pole, Double Throw:
Anyways, electricians would arrange the relays in such a way that would control a process: So say when a float in a tank provided power to a relay, it would then provide power that turned a warning light on and closed a valve: After all, who wants to watch their fresh drafted brew pour all over the floor because Bubba forgot to shut it off:
As you can imagine, this was a major overhaul every time they needed to change something: You generally had to rewire the entire rack and arrange the relays in a different pattern: So the PLC came to life: Instead of relays, there is a computer that you can program: In fact the most common programming language for the PLC is called Ladder Logic The bane of my existence, but more on that later : Ladder Logic is a graphical representation that looks and feels similar to a relay array:
Now to the electrical part: PLC’s control IO through the same basic methods: Why? Because it is consistent and predictable: You don’t have to worry if there’s too much noise in the line because there’s no digital communication with conventional IO: It’s a very forgiving and stable way to identify the state: Now there’s quite a few devices that will either carry digital communications and or provide the state such as HART Highway Remote Transducer Protocol , but I’ll get to those later:
When talking devices, its always referring to itself: So an input is something it is expecting to get data on and and output is something it’s trying to either control or give data to: When I say data, it can be on off Discrete or a variance Analog :
-
DI Discrete IN : An applied voltage represents a true state and lack of voltage represents a false state: This doesn’t have to be a great deal of voltage: It all depends on the PLC and the devices: 12VDC Volts Direct Current and 24VDC are common voltages to use across a control scheme: An example would be if a tank is full, continuity is provided applying voltage to the DI to tell the PLC that the float isn’t triggered this is known as normally closed: This is common because if the wire is cut, it will flag an alarm : Once the float lifts, continuity is broken telling the PLC that the tank is too full and it needs to do something:
-
DO Discrete Out : This is what the PLC uses to output power to a device to control it: So say the DI was triggered and it wants to turn on the air conditioner: It provides power through the DO to a DI on the air conditioner and it turns on:
-
AI Analog In : Lets say we wanted to know how full the tank is or how warm it is in a building: This is done by either adjusting the voltage or the amperage think of voltage like the pressure in your water line and the amperage as the amount of water flow : There’s quite a few different variations in this, but let’s take 0-10VDC as an example: Let’s say at 1VDC the tank is empty not 0VDC so you can tell if you’re getting a signal or if the wire is broke and at 10 VDC the tank is full: The PLC looks at that voltage and determines what the level is: You can convert those voltages to a more human readable format by converting them to EU Engineering Units : So the zero in EU in this case meters, feet, or whatever is measured at 1VDC: The span is the height of the tank, which is measured at 10VDC: Based off of those values you can make more decisions such as when do I take action and when do I just warn: The resolution is how accurate the AI is: It’s measured in steps: Without going into great detail, a 16 bit resolution gives you 65, 536 different possible answers or steps in relation to the voltage: Think about it mathematically, you can have infinite numbers between 1 and 2: The resolution says I’m going to look at x amount of points between 1 and 2:
-
AO Analog Out : If you wanted to tell a smart valve or control the speed on a motor, you can use an AO to go to 50% open or tell the VFD Variable Frequency Drive - used for controlling motors to run at 500RPM you need something more than just on off: AO works off of the same principle as the AI only it’s controlling something instead of monitoring: So in the 0-10VDC example, 5V would be telling the valve to go to 50% open in EU:
-HSC High Speed Counter : You can only look at a DI so often: Just like the resolution, there are an infinite amount of times during a second you can look to see if a DI has changed state: This, of course, is limited by the processor frequency: Generally you don’t need an extremely high rate: Take a valve for instance: You only need to look at it so often as it’s not going to change state in 1 1000 of a second: A HSC is a DI that says I’m going to look at this at a much higher frequency to see if it changes state: So say you have a water rate that uses a turbine: The fins on the turbine passing through a magnetic sensor tells you the rate of the water: In this case you need to look at the state at a much higher frequency:
Hopefully this gives you an idea why basic electronic skills are so handy to have: The logic is converted to different variations of electricity in order to control something else: Once we start diving into the how to do development, it will probably be more apparent: Remember that PLC’s were designed to help electricians and engineers control a process: Next Article I write will start diving into the types of communication protocols used and then on to the languages: